Vacuum Performance
Hose construction determines the ‘hoop’ strength or the relative ability of the hose to resist collapse. Generally, smaller IDs, thicker walls, external reinforcement such as wire wrap or covers and bonding together the hose layers server to increase hoop strength. As the temperature of a hose increases, the hoop strength typically decreases because the hose material softens.
As a hose approaches its static bend radius limit, hoop strength can be adversely affected because the hose profile will go form round to oval. If combinations of these factors exist (i.e. large ID, thin wall, high temperature, extreme bending), hoop strength is reduced further.
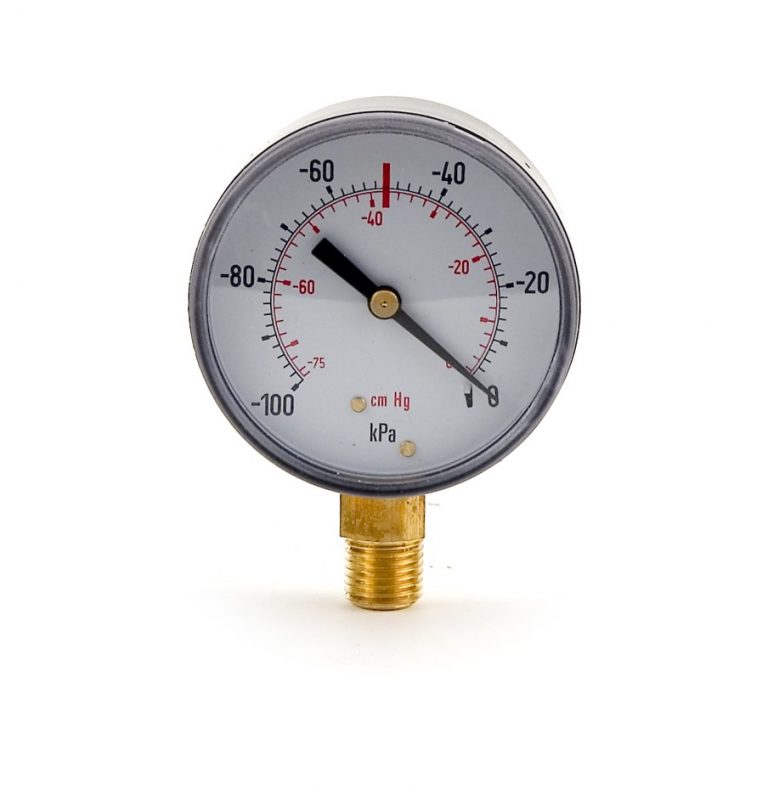
The addition of internal or external springs or bonded covers is the best way to overcome potential vacuum collapse. Certain styles and smaller sizes, smooth bore hoses are rated to 28 Hg at ambient temperature and within specified bend radius.
When vacuum is involved in an application, always determine the expected range of temperature and the potential bending conditions before specifying a particular hose. A common mistake to be avoided involves the use of a transfer hose connected to an ‘upstream’ valve. Since the hose assembly is open ended, the vacuum that is created when the valve is closed can be overlooked.
However as fluid continues to flow downstream, the vacuum created can often exceed 28 Hg, causing even a ‘full vacuum’ rated hose to collapse. In this case, additional reinforcement is recommended.